This project deals with the simulation and experimental validation of eigenstresses in laser-generated composite materials. These materials are used as wear-resistant coatings protecting metallic surfaces against abrasion, erosion, or corrosion. Laser dispersion is the primary process used in this project, where working surfaces of already manufactured parts are coated by adding tungsten carbide powder into the melt pool of a base material. The coating extends the part's lifetime due to the outstanding material characteristics of the locally produced metal matrix composite (MMC). Eigenstresses, which are the residual stresses left in the MMC material after the coating process, shall be investigated and predicted within the framework of this project.
The aim is to find ways for optimizing the stress distribution by numerical investigations. For instance, the influence of processing conditions on the residual stresses may be analyzed to optimize the processing method. The project is divided into multiple stages and tackled with the help of two partners: Bremen Institute for Applied Beam Technology (BIAS) and Heinz Maier-Leibnitz Zentrum (MLZ) in Garching. As illustrated in the overview above, our part can be summarised within two key aspects modeling and simulation, while BIAS will develop the underlying technical process and MLZ will perform neutron diffraction measurements that will help in the calibration of the simulation and for experimental validation.
Funding information and acknowledgement
|
The research project is carried out in the framework of the industrial collective research programme (IGF no. 21079N/3). It is supported by the Federal Ministry for Economic Affairs and Energy (BMWi) through the AiF (German Federation of Industrial Research Associations eV) based on a decision taken by the German Bundestag. |
External links
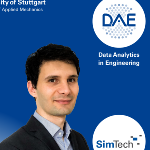
Shadi Alameddin
Dr.-Ing.Postdoc
[Image: Shadi Alameddin]
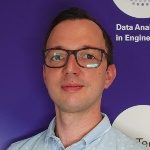
Felix Fritzen
Prof. Dr.-Ing. Dipl.-Math. techn.Head of Department
[Image: Felix Fritzen]